Changes in 3D printing have demonstrated that the technology is advancing more quickly, that processes are becoming more automated, and that production volumes are rising. Although 3D printing technology has many benefits, one of its main drawbacks is its high cost. How to reduce cost of 3D printing?
A few techniques can significantly reduce costs from design to manufacturing and post-processing. In order to reduce the price of 3D printing, this article highlights some useful advice.
Table of Contents
Ways To Reduce Cost Of 3D Printing
1. Product Development
Rapid prototyping, or more specifically, product development, continues to be one of the main applications for 3D printing, and for good reason. Prototyping with 3D printing can significantly lower the cost of developing new products for businesses. Iterating on a prototype only needs a design change because 3D printing is based on digital CAD data.
This implies that companies can produce a product in multiple iterations much more quickly and inexpensively than they could using traditional manufacturing techniques. Faster design iterations result in a quicker product development phase because product flaws can be fixed and improvements can be made earlier on in the design phase, reducing the possibility of expensive errors.
By minimizing the labor required to produce models, tools, and prototype parts, 3D printing can also cut the costs associated with product development. This is particularly true for metal prototyping, which is frequently very labor- and money-intensive. For functional metal prototyping, however, businesses like Desktop Metal and Markforged are providing affordable 3D printing solutions.
Also Read: How to Level a 3D Printer Bed?
2. Lower Material Costs
Another argument in favor of 3D printing as a practical production alternative is the drop in raw material costs. The printing process drastically reduces material waste because raw materials are added layer by layer and only where necessary in 3D printing. 3D printing is resource-efficient compared to subtractive manufacturing techniques, which frequently result in more material waste, especially when high-value materials are used.
3D printing also allows you to reduce the amount of material needed to produce a part, with metal lightweight is a great example of this. Metal lightweighting is the process of using 3D printing to make metal parts lighter. One of the few ways to produce lightweight metal parts affordably is through 3D printing, which is especially useful in sectors like aerospace and motorsports where even one kilogram saved can result in significant cost savings.
A part becomes more expensive in subtractive manufacturing when material is removed from it to make it lighter. Cutting, drilling, and machining all involve additional work and expense. Producing lightweight structures requires complexity, but 3D printing eliminates that expense. The opposite is actually true: the production process is more affordable and efficient the lighter the part.
Related: Is 3D Printing An Expensive Hobby?
3. New Design Opportunities
3D printing enables product designers and engineers to experiment with complex designs and geometries that are unobtainable with any other manufacturing method. This is just one more strategy that forward-thinking businesses can use to cut costs while maintaining product innovation.
Part consolidation is one application of this in action, where designing for additive manufacturing can result in significant cost savings. 3D printing offers an alternative method to traditional manufacturing, which calls for the production of numerous components that must then be assembled to form the final part. The technology allows for the printing of a part that was previously made up of multiple independent components into a single, integrated part.
The use of part consolidation techniques in this way enables manufacturers to realize significant cost savings, including labor costs related to assembly work, decreased inventory costs (as fewer or even no additional components need to be purchased and stored), and lower maintenance costs, as the performance of the part is improved.
GE has so far had one of the greatest successes using 3D printing to cut down on part count. The business used 3D printing to reduce the new General Electric Catalyst turboprop engine’s component count from 845 to just 11. The new design strategy, according to GE, not only lowers the overall cost but also cuts fuel consumption by 20% and the weight of the engine overall. Less parts need to be designed, certified, inspected, and manufactured as a result of the engine’s part consolidation.
4. Low-volume Production
There are many instances where low production volumes do not warrant the purchase of incredibly expensive production tooling. For this reason, traditional manufacturing methods like injection molding are frequently inappropriate for low-volume production. The development of 3D printing as a production tool, however, has created new possibilities for more affordable ways to produce goods in small quantities. The ability to produce parts in small quantities using 3D printing is ideal because there are no setup or tooling costs.
While low-volume production is a compelling application for 3D printing, many businesses are looking for ways to advance the technology’s productivity even further. As an illustration, Betatype, a UK additive manufacturing expert, recently made news for its 3D printed automobile parts. Three hundred eighty-four metal parts could be produced in a single build using two metal 3D printers in just 34 hours thanks to company optimization. To make the same number of parts on a 3D printer that was not optimized, it took 400 hours.
Additionally, the price per part has dropped from $40 to under $4. The company asserts that volumes can approach 1 million parts per year, parts that are more cost-effective and functional, with an installation of 7 machines running this optimized process.
5. Reduced Tooling Costs
By 3D printing production tools like jigs and fixtures, manufacturing costs can be significantly decreased. Jigs and fixtures are frequently outsourced to external suppliers, where they are CNC machined or manually welded and assembled. Jigs and fixtures can be 3D printed on site, which can be a much quicker and less expensive option.
Using Ultimaker 3D printers, Volkswagen Autoeuropa has been producing customized tools for a while. The company can now produce lightweight jigs and fixtures with better ergonomics and performance thanks to technology.
Most impressively, compared to purchasing the tools from outside sources, internal 3D printing at Volkswagen Autoeuropa enables cost savings of over 90%.
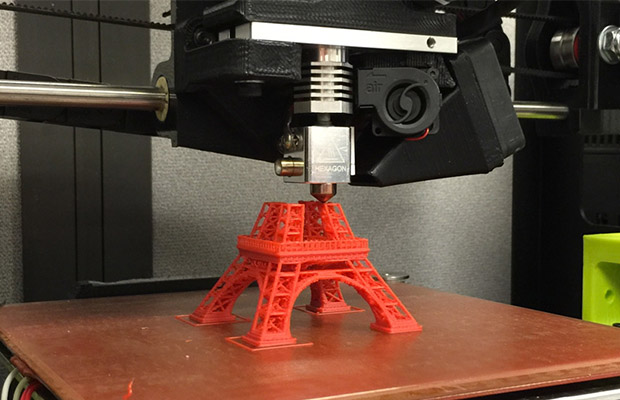
6. 3dD Printing Spare Parts
It can be expensive for many industries to keep a stock of rarely used, low-demand spare parts. There is absolutely no need to keep an inventory of such spare parts with 3D printing. Utilizing technology, manufacturers can produce spare parts as needed, cutting down on the number of parts that need to be kept on hand and lowering inventory costs.
7. Reduce Z-height
3D printers produce parts on a layer-by-layer basis, fusing or bonding one cross-section at a time until the whole object is formed. In powder bed fusion processes like SLS, HP Multi Jet Fusion, and DMLS, layers of powder are melted, and the next layer is created incrementally by the machine. Materials are ejected through a printhead nozzle during extruding and jetting processes. Processes like SLA and DLS strike a balance between layers and cure times. For every layer, which varies from 0.001″–0.013″ in height depending on the process, there is a mechanical movement that can add a lot of time to a part’s build. Hours of additional machine time can be added by combining vertical movement, recoating of material layers, and even incremental automated printhead cleaning.
Keeping printing costs low can be accomplished by reducing the part’s vertical Z-height. It can also be more cost-effective to divide components rather than heighten them. Lower part height reduces the effect of machine activity between layers and concentrates costs more on direct material costs.
Printing is done using printers with various maximum build platform sizes for the SLS, HP Multi Jet Fusion, FDM, SLA, DLS, PolyJet, and DMLS processes at Xometry. These are incorporated into our AI-based quoting algorithms, so parts that can be built horizontally (lying on their side) tend to be more cost-effective than those that must be built with their longest face facing up.
Here are some good “best practices’ lengths to keep in mind when designing your part for a particular process. Generally speaking, staying below these will guarantee a cheaper part. Another way to look at it is that if you don’t use more than half of the space on the platform, you can fit more parts on the build and share some of the overhead costs.
Read More: How Much Power Does A 3D Printer Use?
Conclusion
All stages of 3D printing, including design, production, and post-processing, can be done for less money. If you abide by our advice, you can guarantee that the price of 3D printing is within reason.
Read Next: